Surgical inventory management at Addenbrooke's Hospital
Pioneering the use of RFID technology to centralize and streamline the management of surgical supplies, our solution has freed up time for clinical staff, optimized stock holding and minimized waste at Cambridge University Hospitals NHS Trust (CUH).
In any acute hospital, preparing materials for scheduled and emergency procedures takes up a lot of clinical time. With 1000 beds, 61 wards and 35 operating rooms, Addenbrookes Hospital (part of CUH) is one of the largest hospitals in the UK. Therefore, CUH have massively benefitted from the introduction of RFID technology to their surgical supplies.
Challenges
The main drivers for introducing surgical kitting with RFiD Discovery at CUH were:
- A high volume of stock was held at surgical level tying up resources and taking up space
- There was a lack of visibility of how much stock was actually being used
- The inventory system relied on surgical staff to manually report and log the use of inventory which took up valuable time and was prone to error and omission
- A lot of time was spent by clinical staff handling stock and preparing materials for operations
Solution
CUH had already successfully been using RFID Discovery for a number of years in the Clinical Engineering department to track and locate mobile medical devices. So when Supply Chain Manager, Phillip Lapish, started to look for an RFID system to streamline the process of preparing procedure kits for individual operations, the RFID Discovery Inventory system was an obvious choice.
The Trust is believed to be the first in the UK to introduce a central surgical kitting service using RFID technology, and now prepares around 100 to 120 kits per day for elective procedures plus 50 for emergency and contingency kits. All equipment that surgical staff require for a specific procedure is collated in a patient specific tote box, which contains a Radio Frequency Identification (RFID) tag to allow its unique identification.
Phil comments:
“This enables us to accurately capture the cost of each operation and at the same time allows clinical staff to focus on patient care."
This enables us to accurately capture the cost of each operation and at the same time allows clinical staff to focus on patient care.
How does surgical kitting work?
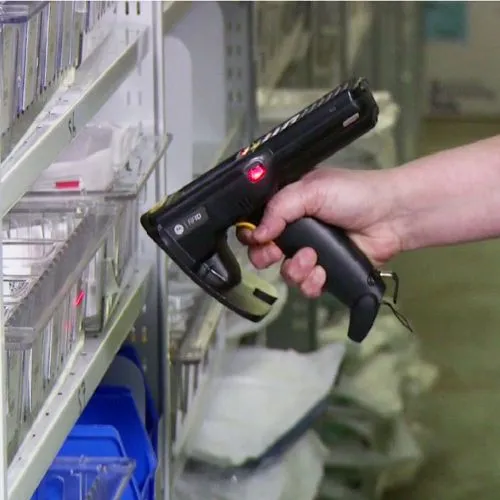
All surgery packs are standardized, for example in Neurosurgery which deals with 400 different procedures there are now 12 different procedure kits. These were developed based on information from leading surgical staff to create a bill of materials required for each procedure type.
Surgical staff add all of their scheduled operations to the Trust’s central electronic patient record system, Epic. This automatically issues all of the required items from the Kitting Store for the planned operations. Through an interface this information is also sent to the RFID Discovery system ready for picking.
The Picking Process
In CUH’s Kitting Store, patient specific totes are prepared by a team of materials handlers who collate all required materials for each operation from the central store using an RFID Discovery handheld scanner gun.
The gun receives a full list of items that have been issued for the particular kit. Using RFID, they capture unique identification numbers on passive RFID tags and to speed up the picking process, the gun displays the exact shelf location for each item. Once complete, the box is sealed with a security tag. Unless all items required have been picked and scanned, the system automatically prevents the completion of the tote. This improves patient safety by ensuring that all the correct items are to hand when needed.
Additional Surgical Stock
In addition to the patient specific kits they receive, each surgical area still holds local stock. In the Top-Up area, low value, high turn-around items such as syringes, needles, dressings and trolley covers are stored. Each operating room also has a store for items of high value but low predictability, such as implants in different sizes or linear staplers. All the items in these stores carry a passive RFID label.
After the operation

When a procedure is finished, totes are sent back to the store and include the patient specific tote box RFID tag, all used wrappers and any unused items. All of the unused items are scanned back into stock and returned to the store.
Phil Lapish comments:
“This returns process enables us to capture the full cost against the patient. It also allows us to track the usage of these items so we can make sure they are replenished for the next time they are required.”
Benefits
The use of RFID coupled with the new processes means that stock replenishment has moved to consumption-led, which means only those items used are re-ordered, eliminating the need to carry a high volume of just-in-case stock.
Reducing stock at surgical level has resulted in a space saving for example Neurosurgery have reduced their store rooms from three to just one.
As a result of the kitting and top-up services, CUH have been able to reduce the per-case cost due to reducing waste and the number of items used for each operation.
Phil gives details:
“The adoption of the kitting process has contributed to a downward trend in consumable cost per case. Our analysis shows that the cost per operation is down by between 2.5 and 7.4% in the specialties where the solution was first deployed such as Neurosurgery.“
Feedback from clinical staff has been very positive. The central kitting solution means that Operating Department Practitioners and nurses don’t have to leave the surgical area throughout the daily list. This releases valuable clinical time and improves patient safety as staff can focus on patient care.
Phil notes:
“Before surgical kitting was centralized, clinical staff would spend an average of at least one hour per day per operating room preparing materials for operations. Whilst we cannot put an accurate figure against the clinical time saved, it’s made a huge difference to surgical staff.”
Helen Torode, Clinical Team Leader, explains:
“It saves a lot of time in the afternoons when you are running a busy list. It’s much easier now; instead of having to free someone up to prepare materials, we just need to get the kits from down the corridor."
Prior to implementation, materials were gathered by a member of the clinical team, often the newest and most inexperienced theatre support worker, based on surgeon’s preference cards. Some of these cards were handwritten and did not include product codes and provided no indication of where to find the required items.
Prior to the implementation of the central kitting solution there was a lack of visibility of what was actually being used for each procedure. With the new solution in place CUH accurately records the cost of the individual operation against the patient number without taking up clinical time.
Centralizing the kitting function has improved the procurement processes at CUH and helps greatly with product standardisation throughout the hospital. In addition, transferring transactional activities from clinical to procurement teams as well as automating the process applied to those transactions has led to a 69% drop in manual purchase orders across the surgical directorate.
An unexpected benefit has been the more accurate reporting of the use of certain items which are excluded from NHS tariffs, such as fibrin sealants. This means that money has been claimed back from the Local Authority for the use of these items relieving the burden on tight NHS budgets.
Phil elaborates:
“With RFID tagging in place, we no longer solely rely on clinical staff to record the use of tariff excluded items and have therefore been able to claim a higher proportion of the costs back. As more of these products get tagged with RFID we are expecting our reporting to improve even further, saving valuable resources for the Trust.”
Implementing unique product identification serves as a step towards preparing for Department of Health regulatory compliance. This mandates every NHS Acute Trusts to adopt GS1 standards for areas ranging from patient identification and product recalls, through to medical records management and procurement by 2019/20.
What's next?
Surgical kitting processes are now used for all of CUH’s 35 operating rooms. A total of 200 different kits are provided for 12 different specialities, including neurology, cardiology, urology and gynaecology.
But Phil and his team continue to fine-tune the surgical kitting processes to maximize benefits. Phil explains:
“For some kits we have had a 100% return rate for particular items over a period of time. So we feel confident that these can be removed from future kits to save time and make the process even slicker.”
The kitting team collects accurate data on how often they top up each of the operating room local stores. This allows them to prove which stock items haven’t been replenished and show where no or little stock has been used from the local stores. This allows CUH to continually modify top-up levels freeing up capital and space by eliminating unnecessary inventory.
Future
Phil is very aware that CUH have only just started to make use of the potential benefits that utilizing RFID technology can bring:
“We currently only track items by programming stock item IDs onto the tags we affix. With the introduction of GS1 standards we will be able to track specific implants down to a serial number to create a completely passive process for matching implants to patients which would be considered the gold standard in terms of patient safety.”
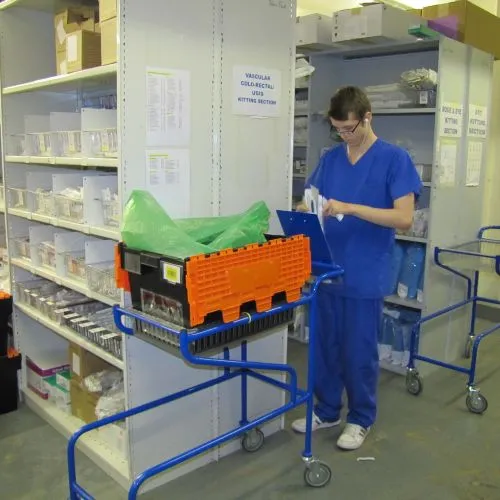
Limited resources in terms of workforce currently restrict the range of procedures the central store kits for and the local items they tag. There are plans to expand into other areas such as Cardiology and Interventional Radiology. Phil:
“This would help increase the level of accuracy we have in capturing tariff-excluded devices thus reducing the financial risk to the trust of not claiming all of the income we are entitled to.”