Reusable PPE tracking
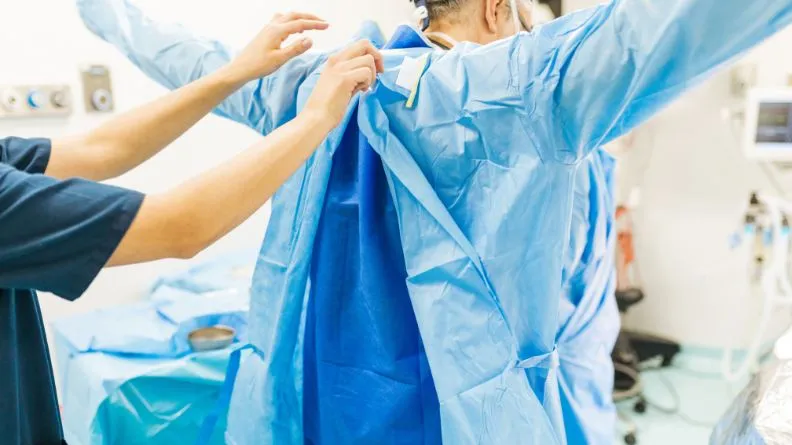
Benefits
Helping to ensure that there is always sufficient supply of PPE available
Due to the growing cost and environmental burden posed by the use of disposable personal protection equipment (PPE) in healthcare settings, reusable garments - in particular multi-use gowns - are becoming increasingly popular. The COVID-19 pandemic heightened the demand for PPE and intensified the need for environmentally friendly alternatives to disposable items.
The challenges
As reusable gowns normally have a limited life span, and are only safe to use for a specified number of washes, it is important to track the number of times they have been laundered to ensure they are still fit to use. In addition, due to the vast number of reusable gowns being used in hospitals and care homes, it can be very challenging to make sure that sufficient stock is available in the right place at the right time. Also, with items going back and forth to external or internal laundry services, PPE can easily be lost, leading to additional expense or even worse - shortages in supply.
The solution
By placing a special passive RFID laundry tag in each gown, the hospital/care home and laundry service provider can track the location of each item, how many they have sent and received and also how many times the items have been used and cleaned. Tags are designed to withstand cleaning procedures and other laundry processes.
RFiD Discovery offers a simple and cost effective solution for laundries and their customers to:
- Automatically track items through the whole cycle of storage, use, transport, cleaning and back into storage
- Monitor stock levels in key locations to ensure sufficient stock is available where needed
- Provide valuable data to inform purchase decisions
- Ensure that the same number of items which were sent to the laundry are returned back after cleaning
In addition, the RFiD Discovery system automatically records the number of cleaning cycles for each item and sends out an alert when reusable PPE is coming to the end of its maximum number of uses. This ensures that the hospital or care home is aware when replacement items need to be ordered so that there is always sufficient stock to cope with demand.
The Process
At the laundry items are:
- Checked in: All soiled textiles are read through an RFID system to let the laundry know exactly what type, from where & how many textiles have arrived to be washed
- Sorted: All dirty textiles are sorted with the support of an RFID antenna. This is key to optimise efficiency & reduce labour cost
- Washed, dried, ironed and folded
- Sorted: All clean textiles are sorted with the support of an RFID. This key to optimise efficiency & reduce labour cost
- Checked out: All clean textiles ready to be loaded on the truck are read by an RFID system. Transparency with the customer is improved & billing can be performed based on reliable data.
At the customer site items are:
- Checked in: All clean textiles that arrive at the customer’s warehouse are read by an RFID system to let the customer know exactly how many textiles have arrived from the laundry & which ones.
- Put into stock: Through a portable reader, inventory at the customer premises is performed to make sure all stock has been accounted for.
- Used by the staff
- Checked out: All soiled textiles are read by an RFID system. No more concern or discussion about lost textiles: the laundry is informed about the customer needs before the textiles get to the laundry.
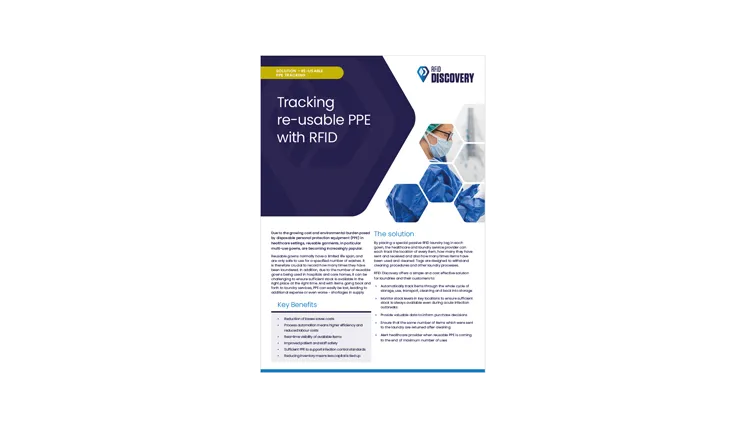
An overview of our PPE tracking solution, helping to reduce the cost and environmental impact of disposable PPE by enabling the use of reusable garments.
Download brochure